“先从电池开始拆吧。因为我觉得只是用底面的螺栓固定住了”。比亚迪纯电动汽车“海豹(SEAL)”的拆解调查已经开始(图1)。
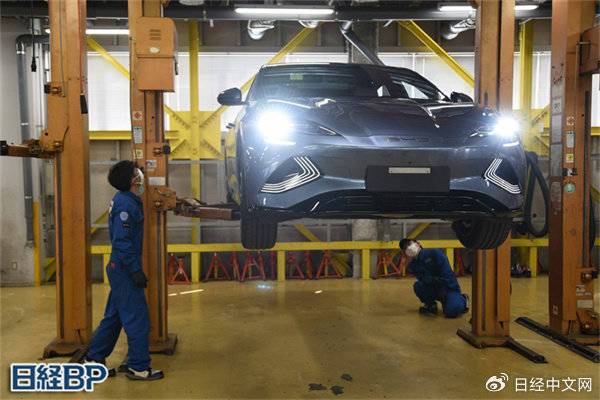
不用说,电池是左右电动汽车性能的重要部件。虽然为了提高能量密度,电池新材料的研发不断推进,但并不会快速提高。某车企的EV技术人员指出,作为延长续航距离的现实办法,各家车企竞相“提高电池的配备效率,尽量增大容量”。
在这种背景下,比亚迪在海豹上采用的技术是“CTB(Cell to Body)”。通过使电池组起到车身构造体的作用,减少部件个数以确保空间,从而可以配备更多电池单元。
比亚迪采用了磷酸铁锂(LFP)类锂电池。与作为正极活性物质的主要成分使用镍(Ni)、锰(Mn)、钴(Co)的三元(NMC)电池相比,磷酸铁锂类的能量密度一般更低。预计是为了弥补这一缺点而采用了CTB。
电池的安装方式与大众“ID.3”不同
为了研究支持CTB技术的电池组和车身,项目组从车身上拆下了配置在底板下面的电池(图2)。拆解是在日本新潟国际汽车大学校(通称GIA)的协助下实施的。日经BP的拆解项目之前已在该校的基地调查了美国特斯拉的EV“Model 3”、“ModelS”及德国大众的“ID.3”。
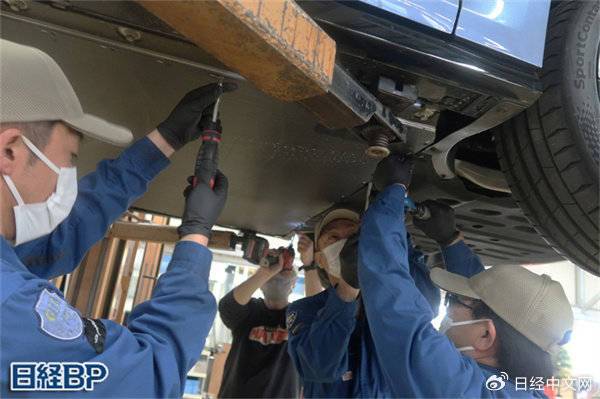
ID.3是将固定电池组的所有螺栓都配置在车体外部的底板下面。这样设计考虑到了在车辆生产线上安装电池组时的操作性,在车辆报废后拆下电池回收利用时也方便取下电池组。
拆解项目组在此前的拆解中了解这些优点,曾经以为比亚迪的海豹也会采用跟ID.3一样的设计。
“哎呀,拆不下来。或许是Model 3的模式……”,负责拆解的技术人员脸上露出困惑的表情(图3)。
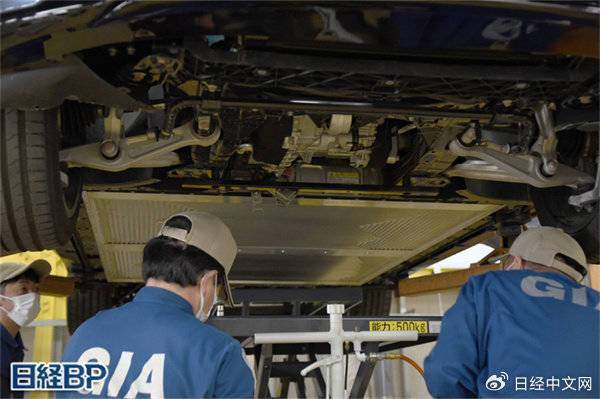
把用来固定电池组的车身底面的螺栓全部拆除之后,海豹的电池仍没有拆下来。拆解Model 3时,必须把座椅和地毯等拆掉,再把固定车身和电池组的螺丝拧下来,才能把电池拆卸下来。这样的记忆再次浮现。
检查海豹的车厢内时,在后座的脚底下、前座稍微隐蔽的位置发现了固定电池的螺栓。这样的话,即便没有准备特殊工具也能拆卸。虽然不需要拆卸座椅和地毯等繁杂的作业,但有的螺栓需要从上端拆除,因此拆解难度介于ID.3和Model 3之间(图4)。
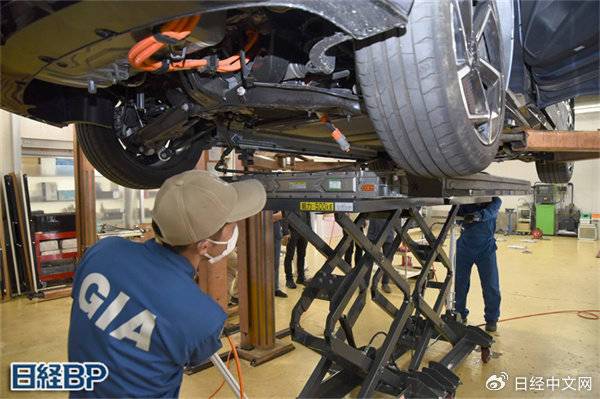
用密封圈来确保密封性
拆下海豹的电池组后,让人感到吃惊的是车身一侧的结构。竟然没有地板。准确来说,是电池组的上表面同时起到了车身地板面的作用(图5)。ID.3和Model 3等大多数纯电动汽车都在电池组上面配置了钢板(图6、7)。
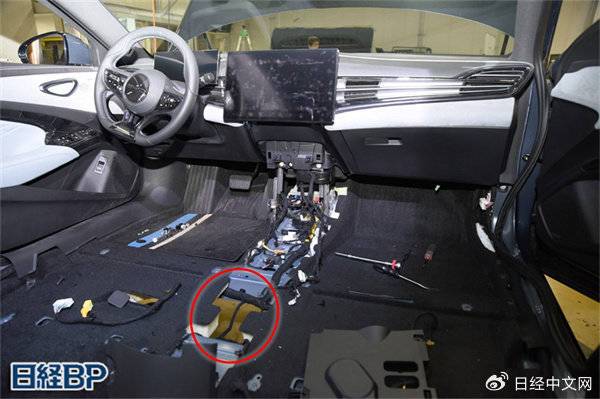
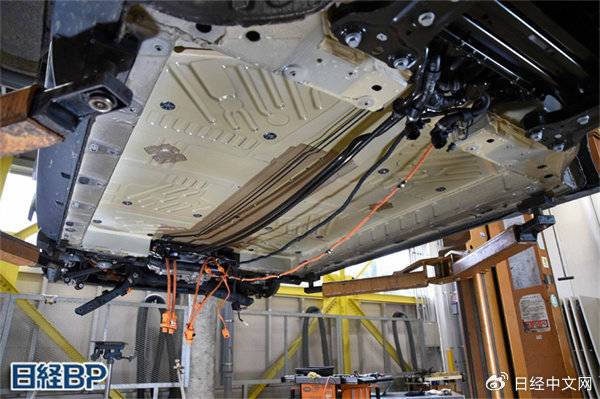
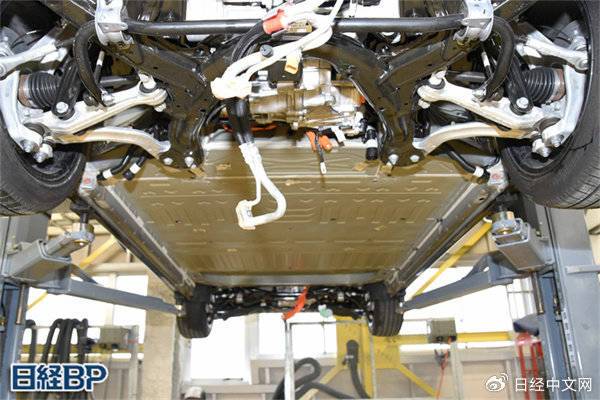
海豹在电池组上配置了横梁(cross member),目的是确保车身的强度以及保护电池避受碰撞冲击。上面是地毯。用发泡材料填充了电池组与地毯之间因横梁厚度而产生的空隙(图8、9)。
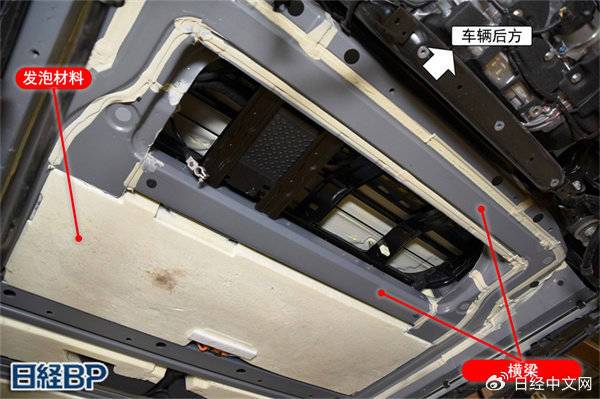
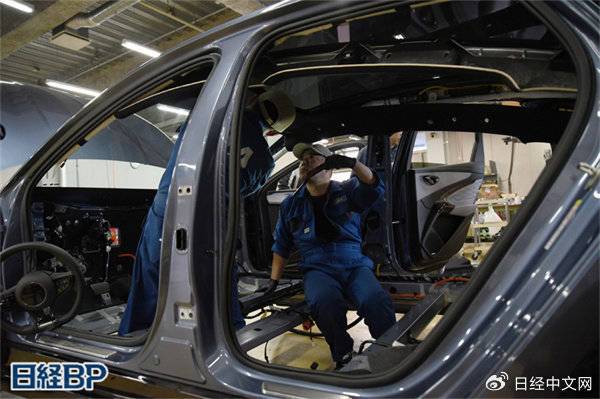
为了防止路面噪声和水等进入,海豹采用了下车体和电池组上部紧贴在一起的结构。具体来说,对电池组上表面的外周进行了彻底的密封处理(图10)。通过拧紧电池组的固定螺栓,使密封圈和下车体紧贴在一起,由此提高了车厢内的密封性。如上所述,电池组上表面同时起到了车身地板的作用,因此很平坦,密封处理并不难。
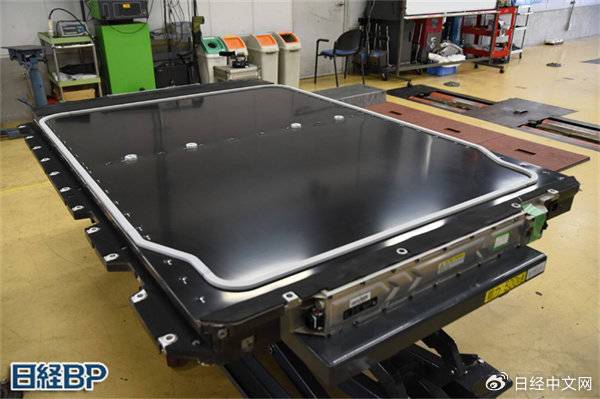
CTB技术让电池组同时起到了车身构造体的作用。通过功能整合减少了零部件数量,而且有利于降低成本。可谓是拥有电池和汽车双重制造商身份的比亚迪才能专门设计出来的结构。